«Import substitution is a trade and economic policy which advocates replacing foreign imports with domestic production», Wikipedia.
The issue of import substitution policy for many countries, Russia included, at certain historical stages may take the forefront position, especially with account of a commodity orientation of this or another economy. Oil & Gas sector constitutes the main source of income, and at the same time is a major consumer of innovations and technical developments.
Some theory and examples.
Import substitution can be declared a central idea of an industrial policy in the three situations as follows:
(1) when a sovereign economy is an importer of a strategic commodity and/or goods and services;
(2) when a sovereign economy is an importer of a substantial mass of traded goods and services, which for a short period of time are subjected to a currency or other type of shock;
(3) import of important (but not strategic) goods and/or services is terminated because of force majeure circumstances of various nature.
Mid of the XX century is considered by economists the actual «birth» date of an «import substitution» term. The concept of import substitution was created and practically applied for the first time in the middle of the XX century in Argentina by the economist Raúl Prebisch.
At the time, based on the concept of the Argentinian economist, a policy was adopted allowing for transfer from commodities export, in which Latin America countries were specialising, to production of industrial products with higher added value (which means more value from export).
National manufacturers got a wealth of privileges and concessions: cheap and long term loans, protective import quotas. Currency control and a fixed exchange rate were introduced. In parallel, a «growth foundation» was created — state monopolies in railway transportation, oil & gas industry, electric power generation sector and communications. But for a number of reasons a 25-year experiment failed.
(1) when a sovereign economy is an importer of a strategic commodity and/or goods and services;
(2) when a sovereign economy is an importer of a substantial mass of traded goods and services, which for a short period of time are subjected to a currency or other type of shock;
(3) import of important (but not strategic) goods and/or services is terminated because of force majeure circumstances of various nature.
Mid of the XX century is considered by economists the actual «birth» date of an «import substitution» term. The concept of import substitution was created and practically applied for the first time in the middle of the XX century in Argentina by the economist Raúl Prebisch.
At the time, based on the concept of the Argentinian economist, a policy was adopted allowing for transfer from commodities export, in which Latin America countries were specialising, to production of industrial products with higher added value (which means more value from export).
National manufacturers got a wealth of privileges and concessions: cheap and long term loans, protective import quotas. Currency control and a fixed exchange rate were introduced. In parallel, a «growth foundation» was created — state monopolies in railway transportation, oil & gas industry, electric power generation sector and communications. But for a number of reasons a 25-year experiment failed.
Norway National Strategy.
To encourage foreign companies to cooperate Norway proceeded from the requirements: foreign partners not only to provide for training of Norwegian personnel, but to work on localising manufacturing processes. This has led to growth of localisation from 10% to 95%. Today’s export share of Norway by 1/3 consists of technology and equipment for oil & gas offshore projects.
For the last two decades Norway has been allocating means not only into development of new oil fields, but into technological improvement which provided for recovery of oil producing formations bringing oil production up to 65%, representing the best result in the world practice.
The efficient oil & gas industry of Norway generated in a rather short historic period, propelled the country to the top of the worldwide market in the area of underwater and drilling equipment, floating oil & gas production systems, storage, shipment and services.
In 1997 the INTSOK association was founded incorporating over 230 Norwegian oil & gas companies. In 2012 the INTSOK association initiated the procedure and made arrangements for the project of technological cooperation between Russian, Norwegian and international companies in the Far North — a RU-NO Barents project.
«Realization of the oil & gas project in Arctic conditions does not only come down to extraction of hydrocarbons. Of no less importance is supporting the process in the long term prospective: its reliability and eco safety. Russia avails of the unique experience of ice conditions observations, which is key to development of central regions of the Russian Arctic part. A Russian nuclear fleet is an important factor as well. Precisely those advanced technologies need to be developed in the country, not trying to invent a bicycle in the areas in which Russian industry lacks expertise.», Vladimir Ryashin, Regional Manager, INTSOK — Norwegian Oil and Gas Partners.
Import substitution in fact means development of the national manufacturing basis and suppliers network. This is why it is important to facilitate their development in the country aiming at higher products added value and further export.
For the last two decades Norway has been allocating means not only into development of new oil fields, but into technological improvement which provided for recovery of oil producing formations bringing oil production up to 65%, representing the best result in the world practice.
The efficient oil & gas industry of Norway generated in a rather short historic period, propelled the country to the top of the worldwide market in the area of underwater and drilling equipment, floating oil & gas production systems, storage, shipment and services.
In 1997 the INTSOK association was founded incorporating over 230 Norwegian oil & gas companies. In 2012 the INTSOK association initiated the procedure and made arrangements for the project of technological cooperation between Russian, Norwegian and international companies in the Far North — a RU-NO Barents project.
«Realization of the oil & gas project in Arctic conditions does not only come down to extraction of hydrocarbons. Of no less importance is supporting the process in the long term prospective: its reliability and eco safety. Russia avails of the unique experience of ice conditions observations, which is key to development of central regions of the Russian Arctic part. A Russian nuclear fleet is an important factor as well. Precisely those advanced technologies need to be developed in the country, not trying to invent a bicycle in the areas in which Russian industry lacks expertise.», Vladimir Ryashin, Regional Manager, INTSOK — Norwegian Oil and Gas Partners.
Import substitution in fact means development of the national manufacturing basis and suppliers network. This is why it is important to facilitate their development in the country aiming at higher products added value and further export.
«Import substitution means equally developing Russian products and technologies, as well as localizing foreign companies’ products and developments in Russia. The most important thing is to develop Russia’s engineering and manufacturing base, allowing for development and production of cutting-edge products meeting the industry’s needs, in Russia.»,
Sergei Arkhipov, Head of Technological Partnerships and Import Substitution, Gazprom Neft PJSC, Bulletin of the Union of Oil and Gas Producers of Russia, 6 March 2018.
Notion substitution.
Various sources quote different numbers related to import substitution in various sectors of the Russian economy; it is worth understanding which equipment exactly could be considered Russian: for example, in oil production about 80% of expenses refer to pipeline transportation expenses (and pipelines are Russian).
Another well known situation: an enterprise is owned by a Russian company, nevertheless it is buying major part of components abroad, its final products are considered Russian.
It is common knowledge that automation constitutes a rather modest share of the whole project value when implemented in the oil & gas sector. But it is the share of high-tech products that defines the efficiency of a production process.
Half-hearted or forced import substitution leads to decline in competition and lower efficiency. The task is to create added value not only for the local market, but globally as well.
While implementing import substitution policy, two equally valuable solutions are worth pursuing: Russian solutions started from scratch, and substitution by way of comprehensive localisation of foreign manufacturers in partnership with Russian companies. Full localisation in the end must be export oriented, i.e. not only assembly, but in the first place component manufacturing in Russia, provisions for service functions and localised R&D.
With this aspect in mind, operational experience of some manufacturers with whom VSP has a long history of cooperation is of interest.
Another well known situation: an enterprise is owned by a Russian company, nevertheless it is buying major part of components abroad, its final products are considered Russian.
It is common knowledge that automation constitutes a rather modest share of the whole project value when implemented in the oil & gas sector. But it is the share of high-tech products that defines the efficiency of a production process.
Half-hearted or forced import substitution leads to decline in competition and lower efficiency. The task is to create added value not only for the local market, but globally as well.
While implementing import substitution policy, two equally valuable solutions are worth pursuing: Russian solutions started from scratch, and substitution by way of comprehensive localisation of foreign manufacturers in partnership with Russian companies. Full localisation in the end must be export oriented, i.e. not only assembly, but in the first place component manufacturing in Russia, provisions for service functions and localised R&D.
With this aspect in mind, operational experience of some manufacturers with whom VSP has a long history of cooperation is of interest.
«We are now creating service technologies, which are related to power engineering and are making electric power safe and reliable. We wish power engineering and industry in Russia be more efficient and safe. We are now dealing with all the aspects related to electrical power engineering, electrification and industrial automation, we also hold strong positions in the «oil & gas» sector, in smart cities solutions and in IT. We have a lot to offer Russia, and we try to manufacture as much as possible here».
Jean-Pascal Tricoire, CEO and Chairman of Schneider Electric, an article «Russia — is a country of engineers and power engineering» in «Vedomosti», dated 14.11.2013.
For the last year Schneider Electric investments amounted to 1 bln Euro. In this respect the role of R&D centre in Innopolice is important: «We engage only local personnel into the project with the aim of joint work with all the leading Russian oil & gas companies», Boris Muratov, Deputy General Director for Russia and CIS.
Another example.
For over 10 years already Emerson has been consistently implementing a localising strategy in Russia. Main business lines cover continuous production expansion, cooperation with local suppliers, research and development of products in Russia, special solutions and options for the Far North climatic conditions, work of engineering centre etc.
A project approach with WIKA — selecting the best in its class product for a concrete application.
During the last few years the VSP company has been developing cooperation with a German company WIKA,
a manufacturer of a wide range of measurement devices and instrumentation products. After launching new high tech production lines in the Moscow industrial «Indigo» park, the Russian specific share of manufacturing exceeded 50%. Pressure gauges from chrome-nickel steel, new models of resistance thermometers, diaphragm seals, and other highly accurate measurement devices. WIKA is planning to reach the depth of localisation for some groups of products up to 70-80% in the long-term.
Another example.
For over 10 years already Emerson has been consistently implementing a localising strategy in Russia. Main business lines cover continuous production expansion, cooperation with local suppliers, research and development of products in Russia, special solutions and options for the Far North climatic conditions, work of engineering centre etc.
A project approach with WIKA — selecting the best in its class product for a concrete application.
During the last few years the VSP company has been developing cooperation with a German company WIKA,
a manufacturer of a wide range of measurement devices and instrumentation products. After launching new high tech production lines in the Moscow industrial «Indigo» park, the Russian specific share of manufacturing exceeded 50%. Pressure gauges from chrome-nickel steel, new models of resistance thermometers, diaphragm seals, and other highly accurate measurement devices. WIKA is planning to reach the depth of localisation for some groups of products up to 70-80% in the long-term.
What must be substituted, what may be substituted, and what is not possible to be substituted in principle?
In the RUPEC overview («Import substitution in chemistry: general principles», published in November 2017., rupec.ru), criteria allowing for defining what must be substituted, what may be substituted, and what is not possible to be substituted in principle so far, are demonstrated on a concrete example.
(Further on some extracts from the overview are presented.)
In order to demonstrate the complexity and a comprehensive character of import substitution it is suggested to consider an example of a currency shock effect in the chemical industry.
Let us consider a technologically possible consistent production chain, along which a nominal raw material (the simplest) by way of several processing stages is turned into a nominal product to be consumed by a nominal end-user. That is, along the chain, the depth of raw material processing, the complexity of products and their market value is being increased. It is necessary to define a criteria, according to which the effect of a currency shock will be considered substantial or not substantial for the market.
(Further on some extracts from the overview are presented.)
In order to demonstrate the complexity and a comprehensive character of import substitution it is suggested to consider an example of a currency shock effect in the chemical industry.
Let us consider a technologically possible consistent production chain, along which a nominal raw material (the simplest) by way of several processing stages is turned into a nominal product to be consumed by a nominal end-user. That is, along the chain, the depth of raw material processing, the complexity of products and their market value is being increased. It is necessary to define a criteria, according to which the effect of a currency shock will be considered substantial or not substantial for the market.
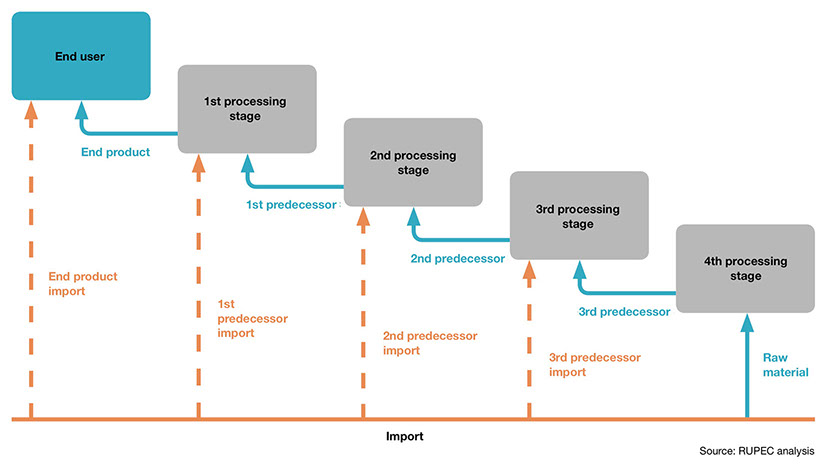
Picture 1. A production chain model in chemistry.
The first damper against a price growth in rubles is the margin of processing companies: with the price exceeding the level of profitability adjusted for the cost structure and with no translation of the increased cost on the price of a product, to continue operation using such an imported raw material means a loss. So, it works against the economics logics. With this, it is the operational margin (the relation of a gross margin to gross revenue) which could be considered a parameter, correlating with the currency shock level.
It is possible to assume that at each processing stage (please see Picture 1) price formation is based on a principle of «cost plus other expenses and profit». With this the cost itself consists of raw materials cost, which may cover imported raw material cost and other components, nominated in rubles, and thus not subject to a currency shock.
Now let us imagine that such a chain does not exist in a national industry, meaning that a final product is imported by the end user. It is quite obvious that with the currency shock, let us say two-fold, a ruble price of a final product for the end user will grow two-fold as well. In most cases this means waiver of import: i.e. the pre-requisites for import substitution of processing stages-predecessors are created.
Further on, let us assume that the industry avails of the two last rings in the chain — the second processing stage, the first stage (please see Picture 1) — and the final product. So, now not the final product is imported, but the second predecessor.
What size the share of raw materials in the cost structure should be responsible for to enable the occurred currency shock «to fade out» in the cited short chain?
We may assume that the criteria of a shock wave «fading» will be a price increase for the final product for the amount of no more than 10%, as this value approximately corresponds to the average profitability in processing industries (b2b model). So, with the resulting shock effect of no more than 10%, the end-user can fully extinguish it at the expense of his profit, not translating it further on the consumer (for example, population).
A complete chain can illustrate more clearly the logics of a fading «wave» of the currency shock in raw material prices.
Assuming there are two manufacturing chains, and in one of them the raw materials share in the price offer accounts for 40% (for all the processing stages), and in the second chain it constitutes 60%. In case the currency shock is presented by a simple two-fold increase of the ruble raw materials cost at a certain processing stage, the relationship of a final product price increase from a processing stage which imports the raw material (and is the first to absorb the currency shock), could be illustrated as follows (please see Picture 2).
As the example implies, with the raw materials share in the price offer accounting for 40%, the currency shock impact on the final product price could be considered insignificant already for up to two-three processing stages.
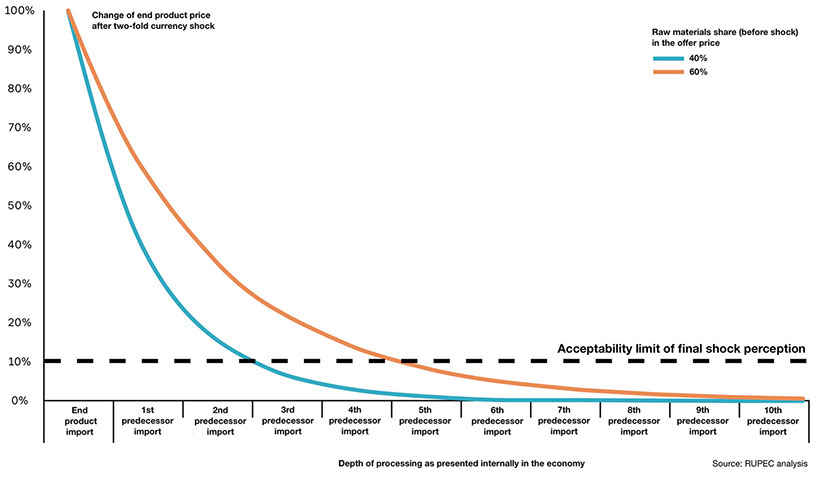
Picture 2. Shock response in the final product price depending on the chain completeness.
Such a relationship is characteristic of high tech processes, in which the share of raw materials is insignificant (under condition of import independence of other price constituents, which is certainly not true for all the cases). In case the raw materials share is rather high, then to minimise the currency shock impact, a consistent chain of four or more processing stages is required.
Should the aim of import substitution as an industry policy be levelling of currency (or any other) shocks for consumers, aiming at maintaining the demand as such, then there is practically no reason in starting facilities distant from one’s own material base and close to end-consumption products.
Talking about chemical and petrochemical sectors, it suggests that realisation of import substitution must be based nearly exclusively on development and «building up» the chains which are already provided with raw materials. In such a case new manufacturing facilities would not import them, or import more or less close predecessors.
The industrial policy itself in the area of import substitution must start with analysis of end industries’ demands in a given chemical product, of «completeness» of manufacturing chains leading to it, and further on analysis of investment prospectives into projects aiming at «building up» existing basis, or monetisation of available raw materials at the lowest processing stages.
The industrial policy itself in the area of import substitution must start with analysis of end industries’ demands in a given chemical product, of «completeness» of manufacturing chains leading to it, and further on analysis of investment prospectives into projects aiming at «building up» existing basis, or monetisation of available raw materials at the lowest processing stages.
Eurotherm solutions as an element of the import substitution chain.
«SIBUR BIAXPLEN» — a subsidiary of SIBUR Holding, is a leading BOPP films manufacturer in Russia availing of manufacturing sites in five regions of total capacity over 180 thousand tonnes per year. The company is actively developing films export to EU markets.
SIBUR takes advantage of a long term growth of the Russian consumer market of polyolefins and a substantial potential for its growth: the consumption level of polyolefins and plastics in Russia remains well below the world average. Moreover, launching new manufacturing facilities would allow to more actively substitute imported products.
A strategic reasoning for development of BOPP films manufacturing, initiated by SIBUR a few years ago, was the need for creating a leading domestic manufacturer, capable of offering new solutions for the underdeveloped home packaging market, at the same time improving the volume of polymers consumption in the country.
SIBUR takes advantage of a long term growth of the Russian consumer market of polyolefins and a substantial potential for its growth: the consumption level of polyolefins and plastics in Russia remains well below the world average. Moreover, launching new manufacturing facilities would allow to more actively substitute imported products.
A strategic reasoning for development of BOPP films manufacturing, initiated by SIBUR a few years ago, was the need for creating a leading domestic manufacturer, capable of offering new solutions for the underdeveloped home packaging market, at the same time improving the volume of polymers consumption in the country.
There was some kind of a paradox in place: «SIBUR» was exporting gases, and then products manufactured from those gases were imported into Russia: plastics, polymers, polypropylene, polyethylene.
Imported packaging materials, BOPP films included, affect the end cost of a product. BOPP technology is considered safe, processing is clean and straightforward. At the same time, the process is rather energy consuming, this is why electric energy management as a factor of price formation is of great importance.
«SIBUR Tobolsk», «SIBUR BIAXPLEN», as well as other manufacturing sites of the holding, use power control equipment manufactured by Eurotherm (Schneider Electric). Higher efficiency and energy costs savings are real benefits the customer receives in return. A combination of reliability, safety and easy operation makes it possible to state that Eurotherm products in process applications offer the best in its class «efficiency / price» ratio.
In the context of import substitution no one has overruled logics of economics, based on analysis and comparison of expected levels of qualitative and quantitative competitiveness.
In spring 2015 «Uralmash NGO Holding» signed a contract with Rosneft for supply of 13 drilling installations of BU 5000/320 EK-BMCh type for cluster drilling of 5 thousand m nominal depth. The drilling installations are modern and fully meeting customer requirements. Technological basis of the holding provides for creation of equipment of the highest quality.
«SIBUR Tobolsk», «SIBUR BIAXPLEN», as well as other manufacturing sites of the holding, use power control equipment manufactured by Eurotherm (Schneider Electric). Higher efficiency and energy costs savings are real benefits the customer receives in return. A combination of reliability, safety and easy operation makes it possible to state that Eurotherm products in process applications offer the best in its class «efficiency / price» ratio.
In the context of import substitution no one has overruled logics of economics, based on analysis and comparison of expected levels of qualitative and quantitative competitiveness.
In spring 2015 «Uralmash NGO Holding» signed a contract with Rosneft for supply of 13 drilling installations of BU 5000/320 EK-BMCh type for cluster drilling of 5 thousand m nominal depth. The drilling installations are modern and fully meeting customer requirements. Technological basis of the holding provides for creation of equipment of the highest quality.
Driller’s control panel — application of Eaton Electric solution.
Offers for oil & gas sector are based on the understanding that operators need to manage and control a process complying with rigid regulators’ requirements and standards in force.
A VSP specialist was invited to a drilling installation of Gasprom-Burenie company in Noviy Urengoy at which sites process solutions by Eaton Electric (former MTL Instruments) are used. The task covered a concrete survey of the installation «in situ», where the equipment supplied by VSP is used, as well as generation of possible offers for the customer to further optimise operational characteristics of equipment.
VSP started cooperation with Uralmash in 2011. At the time, Gecma industrial computers (Gecma is part of Eaton Electric) were chosen by the customer to provide for drilling installations complete set. Industrial computers are used in 5000/320 EK-BMCh and 6000/400 EK-BMCh type drilling installations. The units are installed at the driller’s panel allowing for on-line control of the process.
It was Gecma PC Explorer chosen for operation at innovative drilling installations «Uralmash 6000/400 EK-BMCh Arctic» project for drilling under the Far North conditions.
A «Uralmash 6000/400 EK-BMCh Arctic» unit is an innovative development having no analogues worldwide. The unit is equipped with the cutting edge monitoring and control systems for a drilling process. The unit is fully covered from a crown block down to the rack, and has a combined system of heating allowing for its all weather continuous operation in the Arctic Region.
A VSP specialist was invited to a drilling installation of Gasprom-Burenie company in Noviy Urengoy at which sites process solutions by Eaton Electric (former MTL Instruments) are used. The task covered a concrete survey of the installation «in situ», where the equipment supplied by VSP is used, as well as generation of possible offers for the customer to further optimise operational characteristics of equipment.
VSP started cooperation with Uralmash in 2011. At the time, Gecma industrial computers (Gecma is part of Eaton Electric) were chosen by the customer to provide for drilling installations complete set. Industrial computers are used in 5000/320 EK-BMCh and 6000/400 EK-BMCh type drilling installations. The units are installed at the driller’s panel allowing for on-line control of the process.
It was Gecma PC Explorer chosen for operation at innovative drilling installations «Uralmash 6000/400 EK-BMCh Arctic» project for drilling under the Far North conditions.
A «Uralmash 6000/400 EK-BMCh Arctic» unit is an innovative development having no analogues worldwide. The unit is equipped with the cutting edge monitoring and control systems for a drilling process. The unit is fully covered from a crown block down to the rack, and has a combined system of heating allowing for its all weather continuous operation in the Arctic Region.
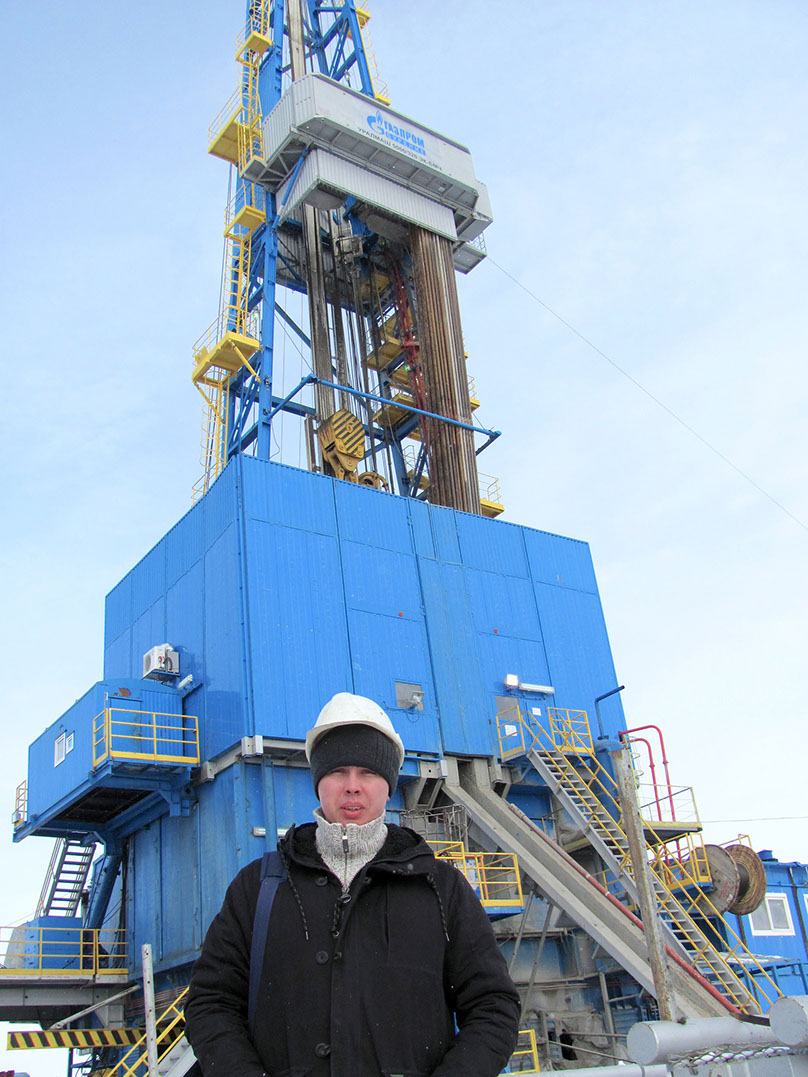
Drilling installation of Gasprom-Burenie company. Business trip to Noviy Urengoy.
«There’s no goal of one hundred percent substitution, …, in order to avoid a monopolistic view of the market and exorbitant prices, you have to have healthy competition. In particular, you have to have a healthy opportunity for not only a competitive market between national and foreign suppliers, but also for them to cooperate in creating new joint solutions. At the same time, you do need to create full-fledged alternative Russian products, fully competitive 100 percent of the time.»
Sergey O.Arkhipov, «Gasprom neft».
Draws upon the contributions of the RUPEC «Import substitution in chemistry: general principles», November 2017, rupec.ru.